Scientists have come up with a technology to recycle used clothes rather than simply burning them
The new technology can separate out the different fibres in the clothes, so that they can be processed and used again.
When you go running in the woods in your running tights, elastane is the reason they fit you so comfortably. Elastane is an elastic material that allows the fabric to stretch and adapt to your body.
But when elastane fibres are mixed with cotton, wool, nylon or other fibres, as is the case in many clothes today, the clothes become almost impossible to recycle. It is extremely difficult to separate out the different fibres, and therefore the materials in the clothes cannot be recycled.
For this reason, clothes and other textiles are among the materials that we are the worst at recycling. Only about six per cent of clothes thrown away by Danish households are recycled. In comparison, 32 per cent of all plastic packaging is recycled in Denmark.
But this may change, says Assistant Professor Steffan Kvist Kristensen from the Interdisciplinary Nanoscience Center at Aarhus University. Together with a number of colleagues, he is behind a new technology that can separate out fibres in mixed fabrics.
“We’ve developed a method to remove elastane completely from nylon. We’re not quite there yet with cotton, because some of the cotton fibres are broken down in the process. But we believe that, with some minor adjustments, we can solve this problem,” he says and continues:
“In other words, we can disassemble the fabric so that we can recycle far more textiles in the future.”
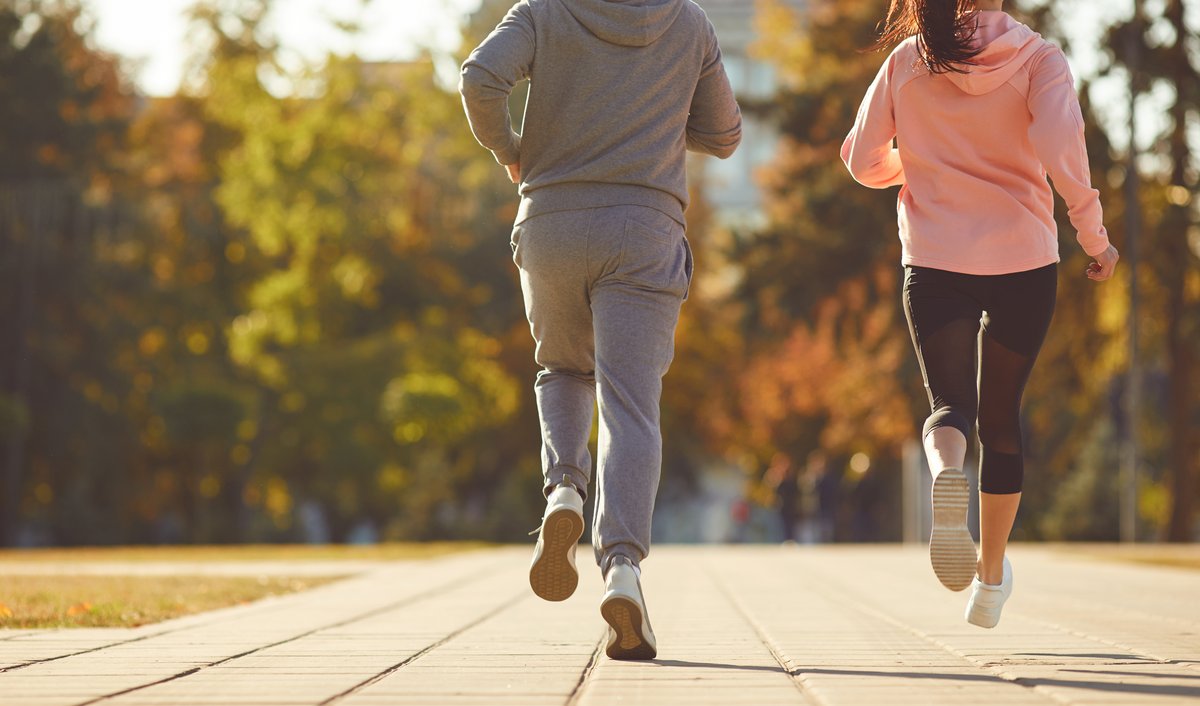
Heating clothes in a large pressure cooker
It is not easy to separate elastane and other fibres once they have been woven together. Clothes are made by winding the main fibres, such as nylon or cotton, around the elastane fibres, which consist of long chains of molecules.
The fibres only break apart if we break the long chains of molecules, explains Steffan Kvist Kristensen.
“The many links in the elastane chain are bound together by a small molecule called a diamine. By heating the clothes to 225 degrees Celsius and adding a specific alcohol, we have found a method to break down the bonds in elastane. When this happens, the chains fall apart and the materials separate.
The whole process takes place in what is in effect a large pressure cooker that we feed the textiles into. We then add a little alcohol and some base and heat it up. Then we let it cook for just over four hours, and when we open the lid again, the different fibres will have been separated.”
Invented during the Second World War
When the Japanese attacked Pearl Harbour on 7 December 1941, the United States not only lost several thousand soldiers, hundreds of aircraft, and many of its largest warships. The country also lost access to about 90 per cent of the natural rubber they depended on so much. Therefore, like the Germans, they began to produce synthetic rubber.
After the war, production of synthetic rubber led to the discovery of a number of derived synthetic fibres that could be used in textiles. One of these fibres was elastane.
In 1958, the chemist Joseph Shivers invented elastane, or Spandex as it is also often called in the United States. Since then, elastane has found its way into more and more of our clothes.
Sources: The National WWII Museum, National Inventors Hall of Fame and CSUSB ScholarWorks.
The secret ingredient is drain cleaner
Because most of the fibres in the clothes need to be recyclable, using harsh chemicals is not an option for Steffan Kvist Kristensen and his colleagues. Instead they use alcohol and add a potassium hydroxide base.
“Potassium hydroxide is one of the main ingredients in ordinary drain cleaner. We found that adding this accelerated the process. It simply increases the speed of the chemical reaction,” he says.
He doesn’t know why this happens exactly, but it does break the bonds in the elastane.
"We're pretty sure that potassium hydroxide increases the reactivity of our alcohol. Either that, or the bonds are broken down slightly by the potassium hydroxide, so it is easier for the alcohol to break them completely,” he says.

Hopes the clothing industry will embrace the technology
So far, Steffan Kvist Kristensen and his colleagues have only experimented with two nylon stockings at a time. The technology is therefore not yet ready for implementation at industrial scale. This will require being able to decompose much larger amounts of clothing.
“We can only scale things up a little because of the limitations in our equipment. So it's up to industry to embrace the technology and scale it up in earnest,” he says.
However, according to Steffan Kvist Kristensen, Denmark does not currently have the facilities to exploit the technology at large scale. You’ll have to look south of the border for this.
"The chemical industry in Denmark is small, but Germany has some of the largest plants in the world. They will most likely be able to use our method to recycle large amounts of fibres from elastane-containing clothes.
If we’re to succeed with this, we need to get the large chemical plants on board. But they must see a business model in buying recycled materials and using them in the production of new fibres. If they don’t, the technology will never take off.”
About the research
Type of study:
Experimental chemistry
External funding:
The study has received funding from Innovation Fund Denmark, the Carlsberg Foundation, the Danish National Research Foundation and the Novo Nordisk Foundation CO2 Research Center (CORC).
Conflicts of interest:
Aarhus University is the co-owner of patent WO2023194469, which covers the chemical process with alcohol that breaks down elastane. The process was developed and patented in connection with another experiment in which the researchers broke down polyurethane, which is the main ingredient in foam for mattresses and sofas. Aarhus University may therefore potentially profit from any industrial interest in the technology.
Link to the scientific article:
Selective chemical disassembly of elastane fibres and polyurethane coatings in textiles
Contact information:
Steffan Kvist Kristensen
Assistant professor
Interdisciplinary Nanoscience Center (iNANO)
Email: skk@inano.au.dk
Phone: +45 28 15 41 00
Troels Skrydstrup
Professor
Interdisciplinary Nanoscience Center (iNANO)
Email: ts@chem.au.dk
Phone.: +45 28 99 21 32
Jeppe Kyhne Knudsen
Journalist and science communicator
Email: jkk@au.dk
Phone: +45 93 50 81 48